From 1977 until the 2003 opening of the Lupu Bridge in Shanghai, China, with its 1815-foot arch, the New River Gorge Bridge was the world’s longest steel arch span.
Carrying Appalachian Corridor L (US 19) across a scenic gorge deep in the hills of Fayette County, the $37 million bridge was a cause for excitement beginning with its June 28, 1973 award as the most expensive single project then ever undertaken by the West Virginia DOH and the Appalachian Development Highway program.
Designed by Michael Baker, Jr., Inc. of Beaver, Pennsylvania, the bridge required 4,759 design calculation sheets. Man hours for these calculations and drawings equal to one man’s working 40 hours per week for 15 years.
Even before the first piece of approach span steel was erected by the American Bridge Division of US Steel in May 1974, stories were spreading among Highways workers about the potential employment of Mohawk Indians, known for their ability to walk the “high steel” of New York City skyscrapers, and a construction insurance policy that projected six deaths because of the structure’s enormous height. (Only one death occurred during construction—on the ground of the gorge’s sloping sides. In a freak accident, a piece of steel fell on one of the forms for the large reinforced concrete pedestals that support the bents of nine land piers below the approach spans, catapulting the men standing on it, resulting in the death of one.)
Rail lines at the bottom of the gorge on either side of the river transported machinery and materials to the site. After vegetation was cleared and old mines were filled with a gravel/grout mix to fill any voids under the footings, concrete was poured for the pedestals under the bents (tapered welded box columns, the tallest nearly 400 feet high).
Erection began with construction of 330-foot towers on either side of the gorge to support twin cableways that could carry loads of 50 tons each or be used in tandem to move the massive pieces of steel in the bent columns and the arch that would cantilever from both sides to meet in the middle (the largest weighed some 90 tons). A helicopter carried the first cable, half an inch in diameter and 5000 feet long, across the gorge between the towers, where it was followed by one-inch cable and finally the 3500 feet of three-inch cable necessary for the cable trolleys. (Guy wires supporting the towers were heavily anchored, giving rise to another story that claimed, when an abnormally heavy wind storm toppled one of the towers early in construction, that the tension released by the wire had sliced through half an acre of nearby trees. In an instant, the trees were cut through cleaner and more uniform than by any lumberjack.)
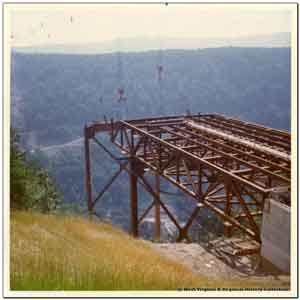
Contributing to the massiveness of the span were over 21,000 tons of structural steel, 1,700 tons of reinforcing steel, 17,000 cubic yards of concrete for the substructure and 6,000 cubic yards of superstructure concrete, for a total weight of more than 88 million pounds.
When the main arch erection began in July 1975, the arch was built slightly higher on each side so that, when the last piece was put into position with the traditional “topping out” ceremony in May 1976, tiebacks on each side could be lowered for a tight fit. Steel boxes totaling over 10,000 tons form the members of the arch, which rises 370 feet. Down at the pins, the vertical sides are steel plates 74 inches high and four inches thick, with the largest joint containing 2,300 bolts.
After the arch was closed, 13 arch towers were constructed symmetrically from the center of the span, with heights ranging from 26 to 305 feet, to support the deck trusses and pavement. Final steel work for the 14-span continuous deck truss over the arch was placed in November 1976. In the spring of 1977 concrete was cast for the parapets, median divider and four-lane deck, which includes eight-foot shoulders in its 69'4" width from curb to curb, and more than 6,000 linear feet of aluminum railing was added.
The steel arch bridge that opened to traffic on October 22, 1977, shortened a previous 40-minute drive over winding roadway to less than a minute. Totaling 3,030 feet in length with its approaches, it has a main span of 1,700 feet, outdistancing the former record-holder at Bayonne, New Jersey by 48 feet (in addition to the second-longest structure, West Virginia has two other steel arch bridges among those listed in the National Steel Bridge Alliance’s 1999 World’s Longest Bridge Spans —the Moundsville Bridge at 24th and the I-470 Ohio River Bridge at 50th).
With a height of 876 feet above the waters of the New River (topping the Washington Monument by 325 feet), the bridge is the highest east of the Mississippi and second-highest in the nation only to Colorado’s Royal Gorge Bridge over the Arkansas River.
That attribute makes the New River Gorge Bridge the perfect site for rapellers and over 500 BASE (buildings, antennas, spans and earth) jumpers on the only day such parachuting is legal. The third Saturday in October is Bridge Day, when a commission closes the structure to vehicles for festivities that include some 250 vendors, luring up to a quarter-million visitors from throughout the world to visit and take a “bridge walk.” (A vehicle attached to the bridge by a bungee cord was thrown over the edge to videotape a TV commercial highlighting its toughness.)
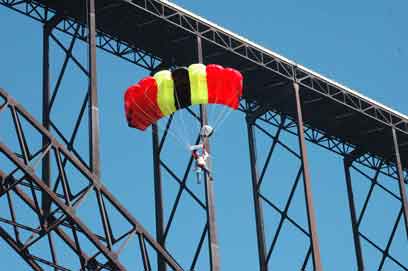
The use of unpainted Cor-Ten steel, a material that weathers to a rust-like protective layer which blends aesthetically with the span’s natural surroundings, saved $300,000 on the original cost and approximately $1 million for each painting that would have been necessary to maintain the bridge. But traditional salt spread on the road surface to remove snow and ice during its first years had an adverse effect on the bridge’s steel, so Highways changed to a deicer that was not salt-based.
Calcium magnesium acetate, a commonly used deicing material that smells like vinegar, nevertheless proved to be both time-consuming and inconvenient. Because of its light weight, it tended to blow off the bridge surface unless it was spread at a speed of 15 mph or less. Thus, in addition to adherence problems, Highways crews created long lines of backed-up traffic with the slow spreading speed. An equipment company provided the solution—a solution of the material mixed with a liquid potassium acetate to adhere much better at speeds up to 50 mph, spread by dump trucks using an attachment combining a precision placement system spreader from one manufacturer with a spreader control system from another.